Table of Contents (click to expand)
Neon lights are made by first creating a glass tubing that is then bent into the desired shape. The inside of the tubing is coated with a phosphorescent material and the tube is then filled with a gas. Two electrodes are placed at each end of the tube and the gas is electrified to create the neon light.
Neon lights are a common sight in today’s day and age. We see them everywhere, from shops and drugstores to advertisements and the bright lights of the Vegas strip. They serve as a highlighting feature for the particular place where they are installed and they really do stand out when seen from a distance. However, unlike most other kinds of lighting, neon lighting differs in the way it’s made. Before we look into the design process of neon lights, let’s take a brief overview of the raw materials involved.
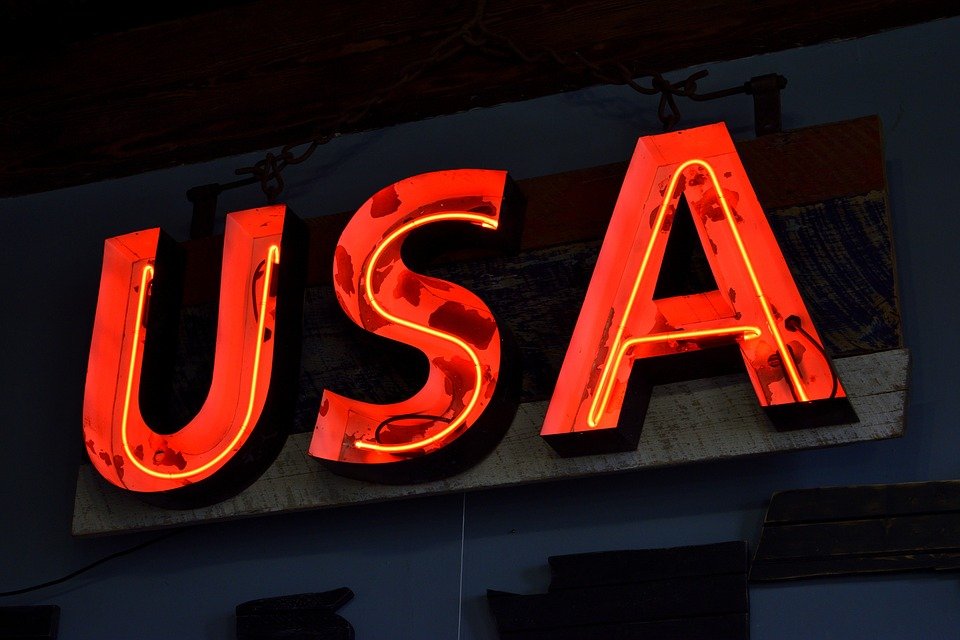
Recommended Video for you:
Raw Materials
Although Neon gas was used to make neon lighting in the past, it is now only used to produce the colors red and orange. Neon lighting no longer solely contains neon gas; in fact, most of the lighting contains Argon or an Argon-Neon mixture. The intensity of the light is changed by adding a small amount of mercury to argon, in the case of blue light. Different colored lights are obtained by coating the inside of the lighting tube with different phosphorescent material. Xenon, krypton and Helium gas have all been used to produce lights for special effects.
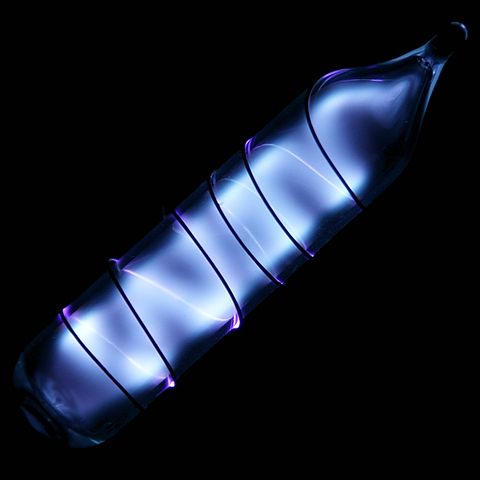
The glass tubing used in the making of neon lights is made from soft lead glass that is easily bendable. Its diameter ranges from 0.3 to 1 inch, and the total length can vary anywhere from 4-5 feet. The electrode at each end of the glass tubing is made of very pure iron surrounded by a glass jacket with one of its ends open. The closed end is sealed to the end of the sign tubing, while the open end protrudes into the tube.
Typical current ratings for neon signs are 30-60 Ma. They are usually connected to transformers that step up the voltage from 120 to 15000 volts. The connection of the neon light to a transformer is achieved through the help of a GTO wire. This wire is also used to connect the individual sections of illuminated tubing in series. The wire is connected to the transformer through an insulated housing made of borosilicate glass with a spring connection on one end.
Manufacturing
The manufacturing of neon signs is primarily a manual process. It consists of bending the tube, attaching the electrodes, and removing the impurities from inside the tube. Finally, the air is removed from the tube and it is filled with the appropriate gas. Now, let’s take a look at the process in more detail.
The first part of the process, as stated, starts with the preparation of the tube. The length of the glass tubing is given a good clean and placed vertically into a coating machine. The machine blows a certain amount of liquid phosphor suspension upwards into the tube and then waits until the liquid drains back into the machine. After this, the tubes are placed into an oven that dries the coating. After the preparation of the tube comes the bending of the tube. The design of the sign the tube is to be shaped into is placed on heat-resistant sheet asbestos. The glass tubing is then carefully heated and softened using a variety of burners. The gas-fired ribbon is used to make curves in round letters and sweeping curves of the script. Smaller hand torches are used to heat shorter lengths. Using the asbestos template as a guide, the tubing is bent by hand. The most astonishing thing in the making of these neon tubes is that tube benders do not wear protective gloves because they must be able to feel the heat transfer and the degree of softening in the glass to determine the right moment to make the bend. To prevent the softened tubing from collapsing, the tube bender attaches a short length of flexible hose, called a blow hose, to one end. While the glass is still soft, the tube bender gently blows into the hose to force the tubing back out to its original diameter.
The third process involves the bombarding of the tube. This process involves the removal of impurities from the glass, phosphors and the electrodes. The first step of the process involves evacuating all the air from the tube. After a certain amount of vacuum is created in the tube, dry air is allowed back into the tube until the pressure is in the range of 0.5-1 mm of mercury. The longer the tubing, the lower the pressure must be. After this, a high current transformer is connected to the electrodes. For a length of tubing that might typically experience 30 mA, 400-750 mA may be used for the bombarding process. The high current heats the glass to about 216°C and the metal electrode is heated to about 760°C.
After the tube is cooled, the gas is pumped into the tube at very low pressure. It must be ensured that there are no impurities present in the gas, as this could produce malfunctions in the operation of the neon light. After the filling of the gas, the aging process begins. It is also referred to as the ‘burning of the tube.’ The aging process is done by attaching a transformer to the electrodes of the neon light. The rating of the transformer is slightly higher than the operating current of the neon light. The full illumination of different neon lights varies. Neon lights may take up to 15 minutes, while Argon might take up to a few hours. The purpose of this is to allow the gas in the tube to stabilize and operate properly. After the aging process, the neon lights are shipped out to their customers in working order!