Table of Contents (click to expand)
Tunnels can be constructed using various methods that depend on the materials used, the tunnel’s purpose, and its type. The most commonly used method involves building a tunnel on the ground and placing it underwater.
Ships and ferries are vulnerable to high tides and storms that can easily swallow them. In 1954, five ferries were lost in the Tsugaru Strait, the body of water between Hokkaido Island and Aomori Prefecture, due to typhoons.
The public was outraged; building a bridge was not an option due to the destructive winds. Therefore, building a tunnel under the water was the safest and most incredible option.
In 1998, the government constructed the Seikan Tunnel, which is not only the longest but also the deepest underwater tunnel in the world. It spans almost 54km and lies 140m below the seabed!

However, the question remains: how were these engineering marvels constructed with all the mud and water that could flow in even from the tiniest of punctures?
Recommended Video for you:
The Tunneling Shield
In the early 19th century, London was a bustling hub for trade in Europe and the world. However, the city’s ports were congested with ships carrying coal and other goods, and the roads were crowded with horse-drawn vehicles. This posed significant challenges, especially with the rise of industrialism. The need for a solution was pressing.
Then, the underwater tunnel emerged as a game-changer, a way to increase the rate of trade and travel without adding to the traffic on the river, revolutionizing the way London conducted its business.
The idea of building an underwater tunnel was considered outrageous at the time. However, engineers realized it was the most efficient solution.
However, there were risks involved. The mud and water from the river could penetrate through crevices and collapse the entire tunnel, which would obviously be disastrous.

In 1818, a brilliant engineer named Marc Brunel developed an ingenious device to tunnel through the seabed without allowing mud or water to seep in. He used what is now called a ‘tunnel shield’, a 40-foot submarine protected by a 3-foot thick wall of steel and bricks. This construction was a remarkable achievement and a testament to Brunel’s genius.
A large drilling machine didn’t excavate the Thames Tunnel between Wapping and Rotherhithe, but people literally chipped at rocks and sand. As the shield moved forward, workers in the front, who were exposed through small cavities, would dig while the people behind would line bricks along the tunnel that had just come into being. The workers had to develop two outlets, one for disposing of mud and sand and another for water.
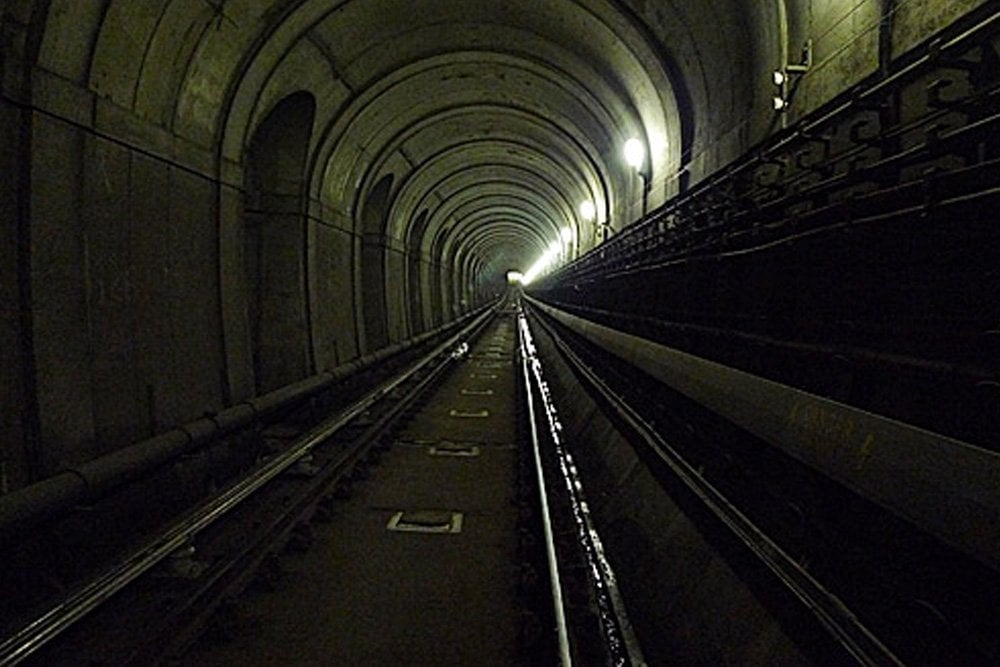
What was predicted to take only three years actually took around 18.
Finally, the bricks were fortified by concrete, and the development of a tunnel capable of bearing horse-drawn vehicles – and later trains – was finally complete. The tunnel is still a crucial part of London’s Overground railway network. For a brief period, it was deemed to be the 8th wonder of the world.
The Prefabricated Tunnel And ‘Moles’
Constructing a tunnel on land and then placing it underwater instead of building it while simultaneously digging is possible. This method involves creating the tunnel in segments sealed with bulkheads to ensure they float. Additional weights are used to force the segments to sink, placed in a long, narrow cavity that runs the length of the tunnel.
The cavity is developed by dredging and grading the trench before constructing the segments. After all the segments are joined, the water between the joints is pumped out hydraulically, and the tunnel is sealed. The Ted Williams Tunnel in Boston, which connects the southern part of the city and Logan Airport, was built using this method.
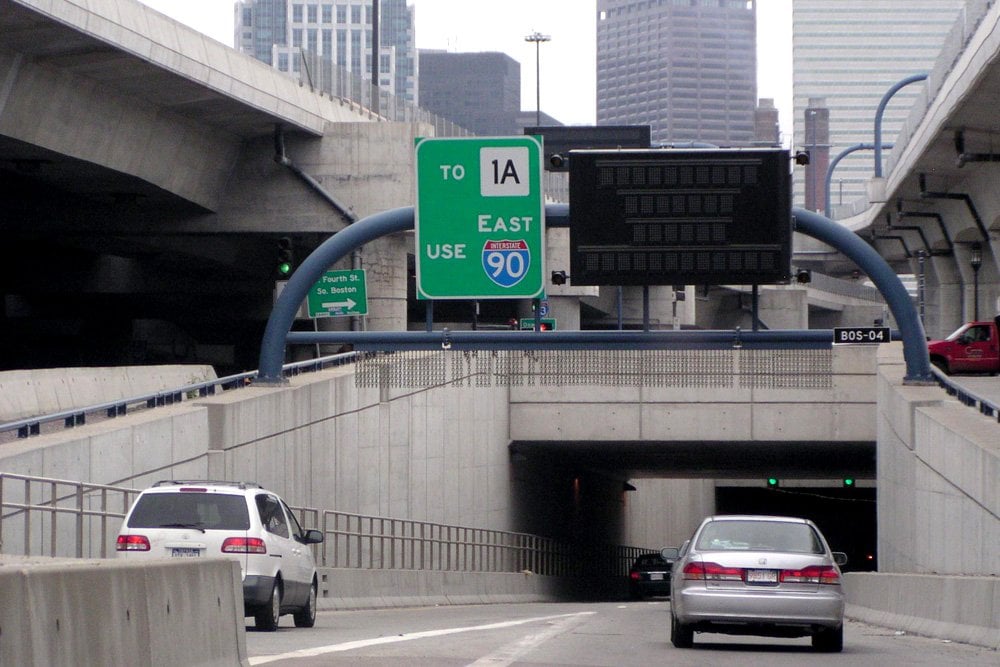
Twelve segments, each 325 feet long, were joined to form the tunnel, and each segment already contained a fully constructed road.
While cost-effective, this technique has several disadvantages:
- Engineers must be extremely cautious when sinking the segments, as even a slight misalignment can have devastating consequences.
- While the tunnel is built under a trench, some segments may face the water and be exposed, which could result in horrific accidents if struck by sunken ships or anchors.
- Digging the channel’s bed has detrimental effects on the environment and ecosystem.
The most convenient method is a Tunnel Boring Machine (TBM), a gigantic drill. The Channel Tunnel, connecting the UK and northern France, was built using TBMs, which excavate tunnels by cutting through rocks and strata with rapidly rotating blades.
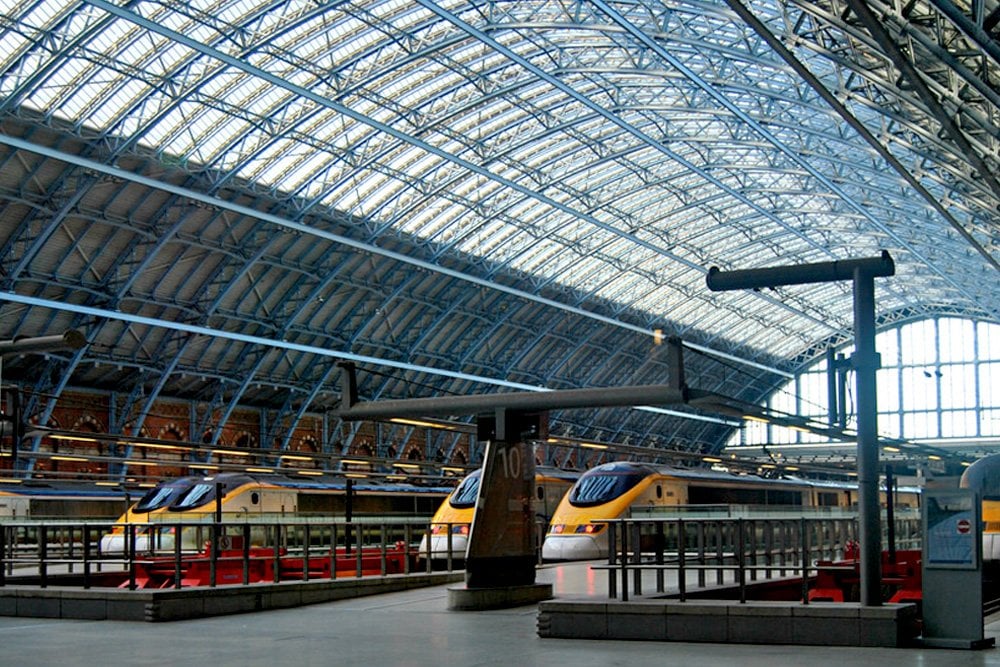
Of course, this convenience is expensive. Furthermore, a single machine, which costs millions of dollars, cannot build a tunnel by itself. The Channel Tunnel required 11 of them to build. However, while the preferred method of building a tunnel relies on convenience, the speed of construction, and expenditure, the most important factor remains the nature of the soil that must be penetrated. As a result, no technique can be crowned to be the absolute best.
Last Updated By: Ashish Tiwari
References (click to expand)
- Eisenstein, Z. D. (1994, July). Large undersea tunnels and the progress of tunnelling technology. Tunnelling and Underground Space Technology. Elsevier BV.
- Hong, K. (2017, December). Typical Underwater Tunnels in the Mainland of China and Related Tunneling Technologies. Engineering. Elsevier BV.
- Pidić, A., Aasbøe, E., Almankaas, J. S., Wulvik, A. S., & Steinert, M. (2018, August 26). Low-Cost Autonomous Underwater Vehicle (AUV) for Inspection of Water-Filled Tunnels During Operation. Volume 5B: 42nd Mechanisms and Robotics Conference. American Society of Mechanical Engineers.
- Tunnelling: Mechanics, methods, and mistakes.
- 6 Innovative Underground Technology and Engineering for ....