Table of Contents (click to expand)
A chassis is the primary load-bearing framework of any automobile. It also serves as the mounting point for various components of the vehicle.
If you have ever seen a rally championship, you know that while the car might look similar to its road-going counterparts, it has stronger underpinnings that allow the driver to subject it to some pretty severe abuse.
Recommended Video for you:
What Is A Chassis?
A vehicle experiences a multitude of static and dynamic loads, all of which can be allocated to the categories stated below:
Static loads, such as the weight of mechanical and other components, passengers and luggage, or dynamic loads such as:
- Vertical and shear loading, when driving over an uneven surface
- Inertial stresses due to acceleration and braking
- Centrifugal forces when taking turns, especially at high speeds
- Torque from the engine and transmission
- Lateral forces in the event of a collision, crosswinds etc.
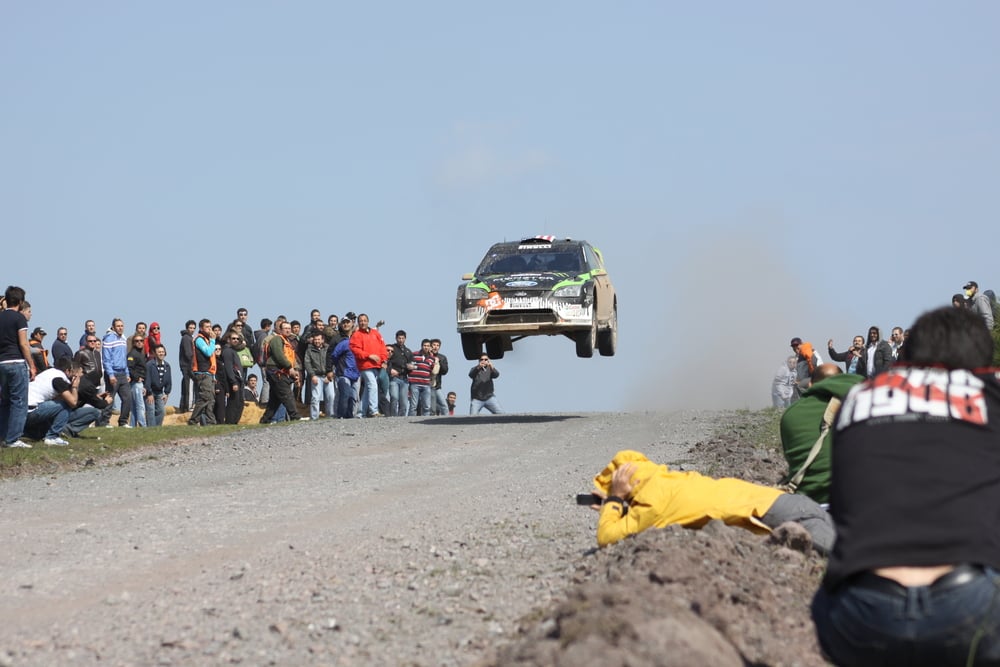
In order to withstand loads like these, it is important for the automobile to have a sturdy load-bearing framework that does not deflect or distort upon impact. This framework is known as a chassis.
Even though we may not be rally racers ourselves, our vehicles also face a multitude of stressors on a regular basis. The chassis of any automobile is therefore a component that involves intensive engineering.
A chassis is designed to suit a certain application, which is achieved by design trade-offs. While a vehicle chassis may occasionally withstand forces, it is not designed for prolonged exposure to such loads, which can often result in catastrophic failures. For example, a truck cannot take turns like a race car without the risk of flipping over on its side. Likewise, a race car cannot be made to haul heavy loads without the appropriate architecture to support it.
Materials Used To Form The Chassis
Traditionally, chassis have been fabricated from carbon steels. Following the need for developing lighter vehicles, there was a shift to aluminum alloys that were as strong as their predecessors, but not as heavy.
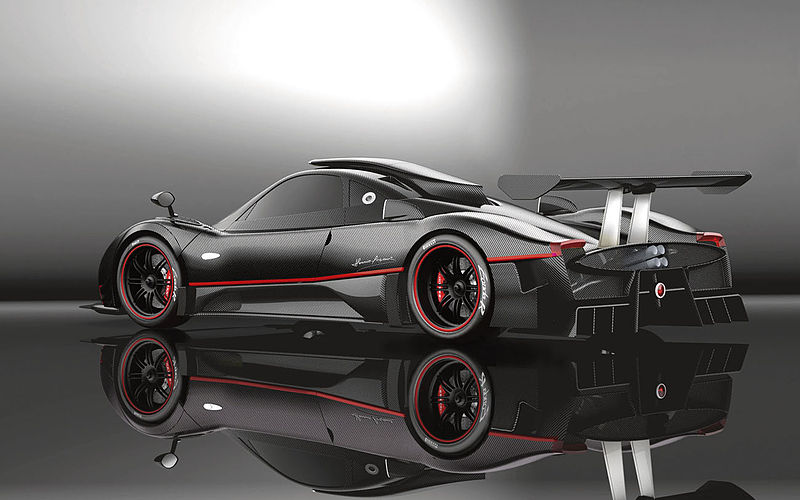
However, with the advent of carbon composites, such as carbon fiber and carbon-titanium alloys, the weight of chassis has reduced significantly while also improving in strength. While carbon composite chassis are commonly seen in sports cars, they have yet to be employed in regular vehicles.
Cross-section Of Chassis
A chassis framework comprises various links that are joined together, either by forming or welding. In order to maximize resilience and load-bearing capability, while not increasing their own weight, chassis links have cross-sections.
Chassis cross-sections can either be open-ended, such as a C- or U-shape, or closed, such as a box shape or a tube.
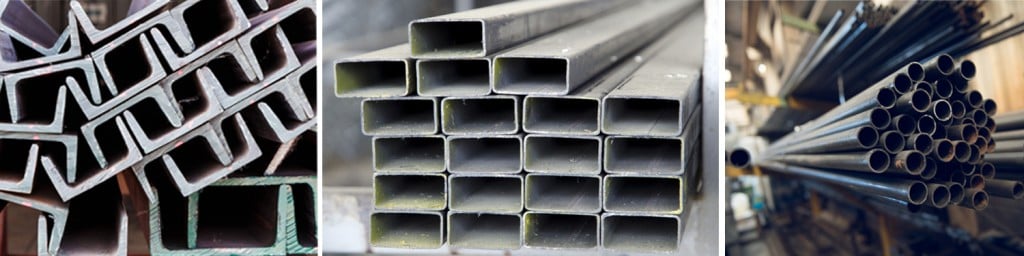
While open-ended chassis frames can bear heavy loads, they are not as good when it comes to transverse loads. Modern constructions often involve open cross-section reinforcement for closed cross-section chassis for extra support. Tube-type chassis are primarily used in two-wheeled vehicles.
Various Types Of Chassis
While the chassis of double-track vehicles, such as cars and trucks, share commonalities, single-track vehicles like bicycles and motorcycles have a profoundly different chassis design.
1. Single-track Vehicle Chassis:
Backbone Frame
The frame is a spine that simply connects crucial components, but does not support them. The engine is bolted to the frame at one end and remains suspended at the other. This is typically employed in low-cost motorcycles that have a small engine and do not see heavy usage.
Cradle Frame
A cradle frame is similar to a backbone frame, except that it uses an additional tube link support for the engine. The ‘cradle’ can either be a single tube or double tube, depending on the size of the engine fitted to it. A single cradle frame is cost-effective to manufacture, but does not exhibit superior load-bearing and handling properties at high speeds. A double-cradle frame comprises two tube links that hold the engine. They exhibit better load-bearing and handling properties due to these two links.
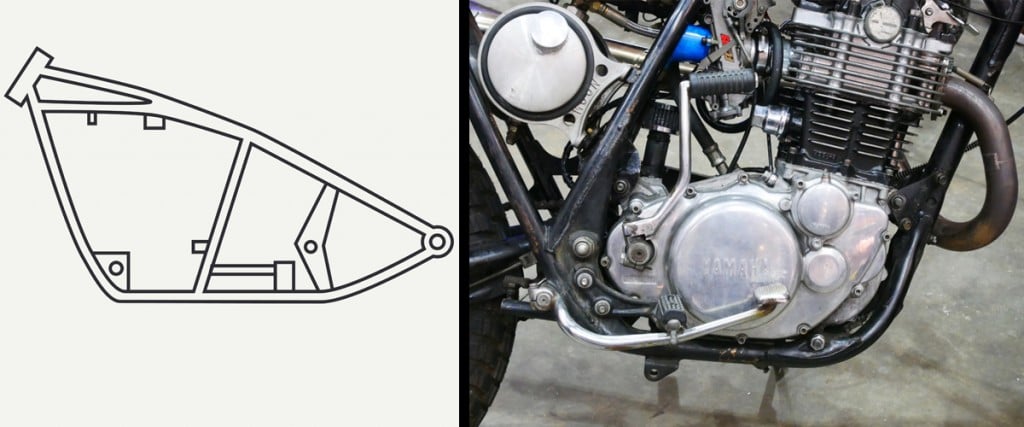
Perimeter Frame
A perimeter frame is fashioned out of box frames, rather than tube links, and connects the steering link to the rest of the body using the shortest possible linkage. The engine is suspended, as in a backbone frame, but the structure makes this style more conducive for high-performance applications.
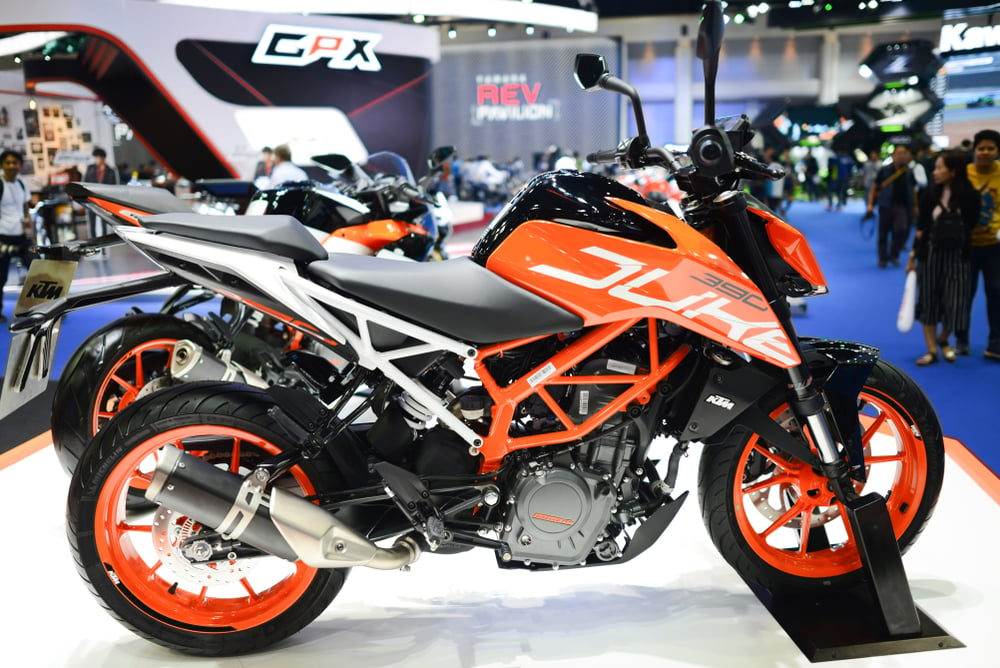
A trellis frame is an iteration of the perimeter frame that employs tubes instead of a box frame to reduce the overall weight of the construction. Like a perimeter frame, it sees usage in high-performance motorcycles.
2. Double-track Vehicle Chassis:
Ladder Frame
This chassis is composed of two parallel beams connected to each other by means of cross members to make a ladder-like structure. All components, including the body, are mounted on the ladder frame. Vehicles with a ladder frame chassis have a higher center of gravity and exhibit superior vertical load-bearing capabilities. However, they are not very resistant to cornering forces that are encountered when taking turns at high speeds. While they were once popular in older cars, they are now commonly found only in trucks and buses.
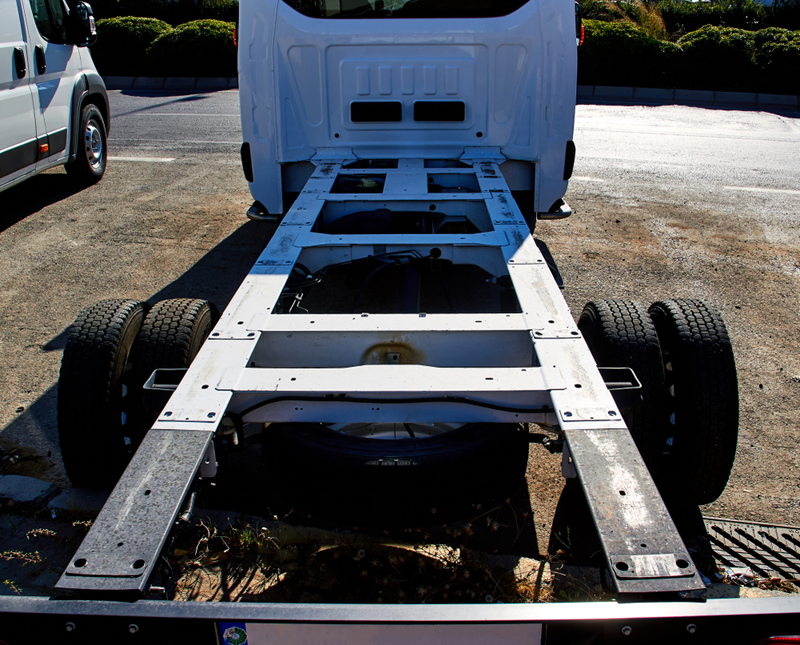
Unitized Body Chassis
Instead of fixing a body that does not have load-bearing capabilities on a frame, a unitized body chassis makes the body an integral member of the frame. Such a chassis is inherently safer and has a low center of gravity. It keeps the vehicle stable when cornering at high speeds and responds well to warping loads. Due to the entire body being a load-bearing member, collisions are absorbed effectively, which minimizes the risk of injury during mishaps.
Unitized body chassis are also known as monocoque chassis and are almost ubiquitously employed in cars.
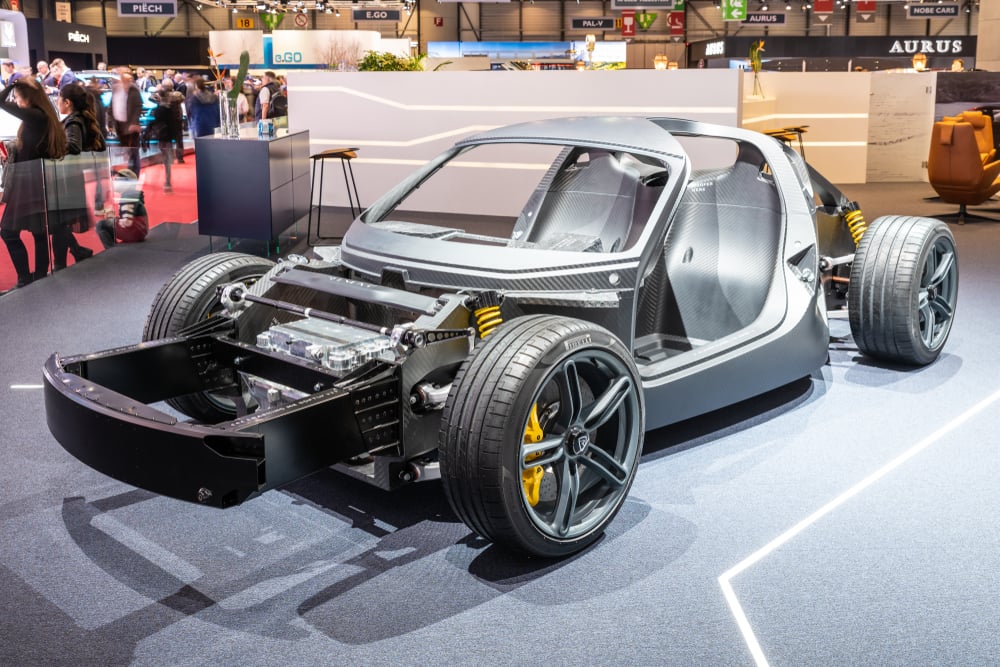
Special Purpose Chassis
These are iterations of either ladder-on-frame or monocoque chassis. They are purpose-built and are not seen in commercial usage. One such example is the carbon fiber monocoque chassis, commonly referred to as a carbon fiber tub, which is used in Formula 1 racing.